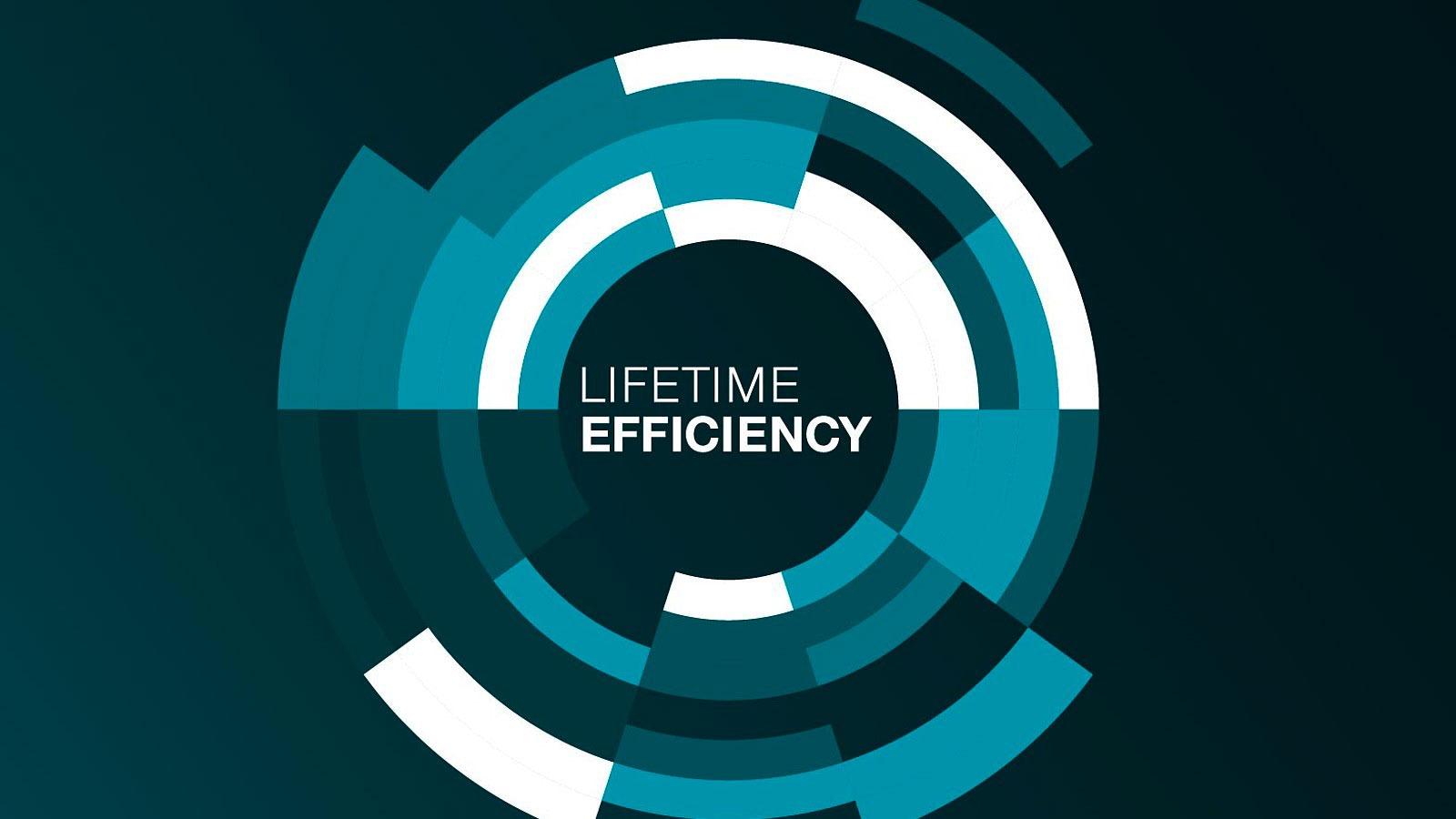
Optimizing production is a continuous process. At Fette Compacting, it starts with an analysis of the production requirements and conditions in the Competence Center and continues along the entire life cycle of machines. “Even if no specific bottlenecks or quality problems arise, practically every ongoing production process harbors untapped potential,” claims performance consultant Jochen Gäth. This is indicated by several examples of his last optimization project at a company producing hundreds of different products at a site in eastern Germany, some of them displaying complex features. Type 3090i and 2090i machines from Fette Compacting are in operation. Jochen Gäth took a closer look at all of the processes and machines on site.
Optimal handling of tableting tools
Gäth identified an initial lever in the area of Tool Management. Accordingly, for the purpose of better parts planning he recommended recording more information on the number of tablets produced and on the respective product per tableting tool as well as improved documentation of the standard processes. An optimized polishing time for standard applications also led to 50 percent savings in time. Furthermore, an extended polishing time was to be applied for products to be bonded, ensuring a significantly smoother surface. None of these measures incurred external investment.
Refresher training for fewer rejects
Next step: production ramp-up. Gäth detected a lack of pre-filling of the segment holes when the machine was ramped up. Pressing force control activated at the same time caused unnecessary wear to the punches as well as a high reject rate. It was possible to reduce the number of bad tablets from 24,000 to 5,000 per batch. Overall annual savings amounted to around 1.2 million tablets. Among others, Gäth recommended regular, in house refresher training for operators in order to guarantee optimal handling.
The very best for every product
On account of the high number of products, the first step entailed Fette Compacting concentrating on a few particularly promising or complex tablets. The latter included a preparation for reducing cholesterol levels which tended to bond at the score in particular. Ultimately, an adapted configuration of the Fill-O-Matic with numerous process-optimized components and machine parameters led to improved filling. The customer was not at all aware of this untapped potential as the fundamental production targets were being reached. But now he can benefit from 40 percent more output in the future.
Preparation is everything
The next optimization step involved potential automation to reduce personnel requirements for night shifts. However, an analysis indicated that the process could be designed efficiently in a much easier way. Gäth discovered that – in order to free up personnel capacities for other tasks – better preparation of the machines for the night shift would suffice. This ensured that the operators could concentrate solely on operating up to 5 machines instead of possibly being responsible for both operation and conversion of two machines at the same time.
And last but not least, Gäth subjected the maintenance processes to a risk-based analysis. As a result, it was possible to streamline annual maintenance by deleting maintenance measures already being applied on a regular basis from the annual maintenance – despite unchanged quality and performance. Consequently, the annual time required for each machine without calibration was reduced from 24 to 12 hours.
“We were able to identify numerous optimization levers in all areas of the production process and then implement the corresponding measures. Often in areas which the customer would never have thought of. This is exactly what distinguishes Lifetime Efficiency: making continuous use of the entire range of analysis in order to guarantee efficient production over the long term,” concludes Jochen Gäth.
Checklist
Seven levers for efficient production
1. Lifecycle: Have the entire life cycle of all machines, processes, and settings regularly reviewed for untapped optimization potentials.
2. Tableting Tools: Ensure that wear data are collated systematically and comprehensively and that standard processes are documented in a comprehensible manner for all operators.
3. Machine start-up: Conduct regular refresher training with your operators to achieve optimal results at all times.
4. Product management: Ensure that the equipment, setting, and parameters are selected in such a way that they are optimally coordinated to the product as this is a decisive factor for complex products in particular.
5. Process equipment: For each process, check whether manual work steps can sensibly be replaced by mechanical ones.
6. Automation: Before considering automation, you should ensure optimal coordination between personnel and processes.
7. Maintenance: Document regular maintenance measures as these steps can be saved during annual maintenance.
Would you like to take a closer look at your production? Talk to our Performance Consultant Jochen Gäth:
Jochen Gäth
Phone: +49415112331
Email: JGaeth@fette-compacting.com