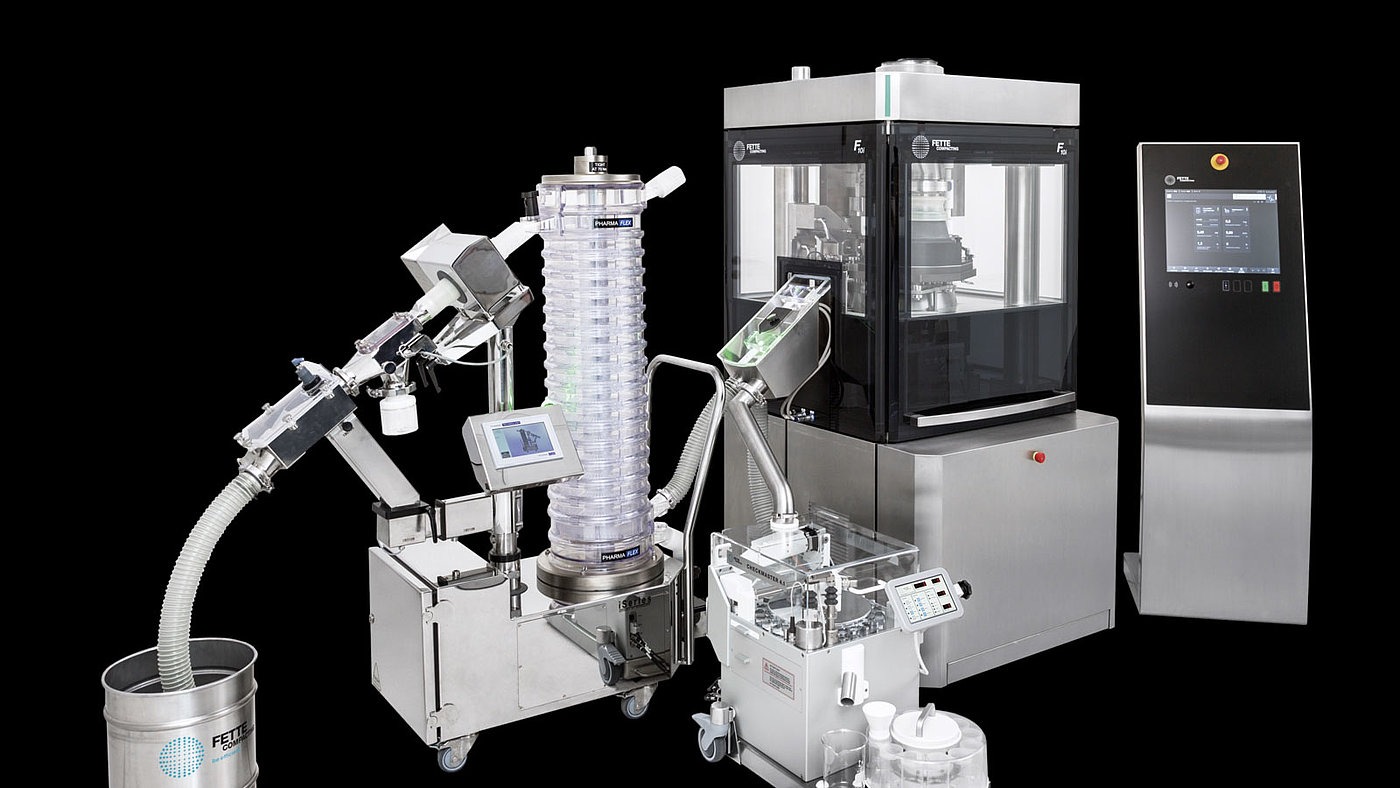
Mr. Friedrich, the pharmaceutical industry is changing. The coronavirus crisis has accelerated many of these developments. What does this mean for machine designers such as Fette Compacting?
Friedrich: Corona confronts our customers and us with new challenges. More than ever before, manufacturers must ensure the population‘s supply of medicines and continue to optimize the efficiency of their production. In this context, the performance of the entire machine park is relevant. With the F10i, we have developed a smart machine together with our customers that can be quickly digitally integrated, supports frequent product changes, and has been optimized for clean operation.
Mr. Gierds, what features does a tablet press need to have for this?
Gierds: A major role is played by connectivity, i.e. exchanging data with other machines within the meaning of Pharma 4.0. That is why the F10i offers the technical prerequisites for state-of-the-art production environments, including process equipment integrated via plug-and-play. The open interfaces meet the usual standards of industrial automation with the result that the machine can be easily integrated into a manufacturing execution system and connected to the Internet of Things.
Just how important is the user friendliness of a tablet press?
Gierds: The easier it is to operate a machine, the more efficient production will be. For this reason, the new i Series ensures that even less experienced operators have a clear overview of all parameters and can avoid operating errors. This is aided by a Human Machine Interface (HMI), whose terminal permits intuitive control, monitoring, and documentation of the machine and process equipment. At software level, a Workflow Operation Wizard guides users through standard procedures.
Friedrich: Additional support is offered by the SmartInterface. Thanks to this server-based application, operators can monitor their production processes in real time using mobile end devices, enabling the production manager to retain full overview of manufacturing independent of location and deploy his personnel in a more proactive manner. This is a clear advantage, particularly in times of restricted contact necessitated by Corona.
Apart from the digital opportunities, how much efficiency potential is offered by the mechanical design of the machine?
Gierds: A lot. We have made sure that the new i Series is compatible with the tablet presses of the old i Series. Both have the same parts with product contact. Turret dies and segments as well as turrets can be easily exchanged. This horizontal integrability reduces the effort associated with validation, qualification, and spare parts storage which, in turn, translates into cost savings.
Are you currently observing any other trends on the market?
Friedrich: Operator protection is increasingly gaining in importance. Nowadays, it is longer about merely protecting operators from toxic substances. Fully dust-free workplaces are the new standard. That is why the standard tablet presses in the new i Series are already consistently dust-free – from the press room to the connections between the machine and process equipment. The tablet press can also be upgraded to include the appropriate containment package for active or highly-active substances.