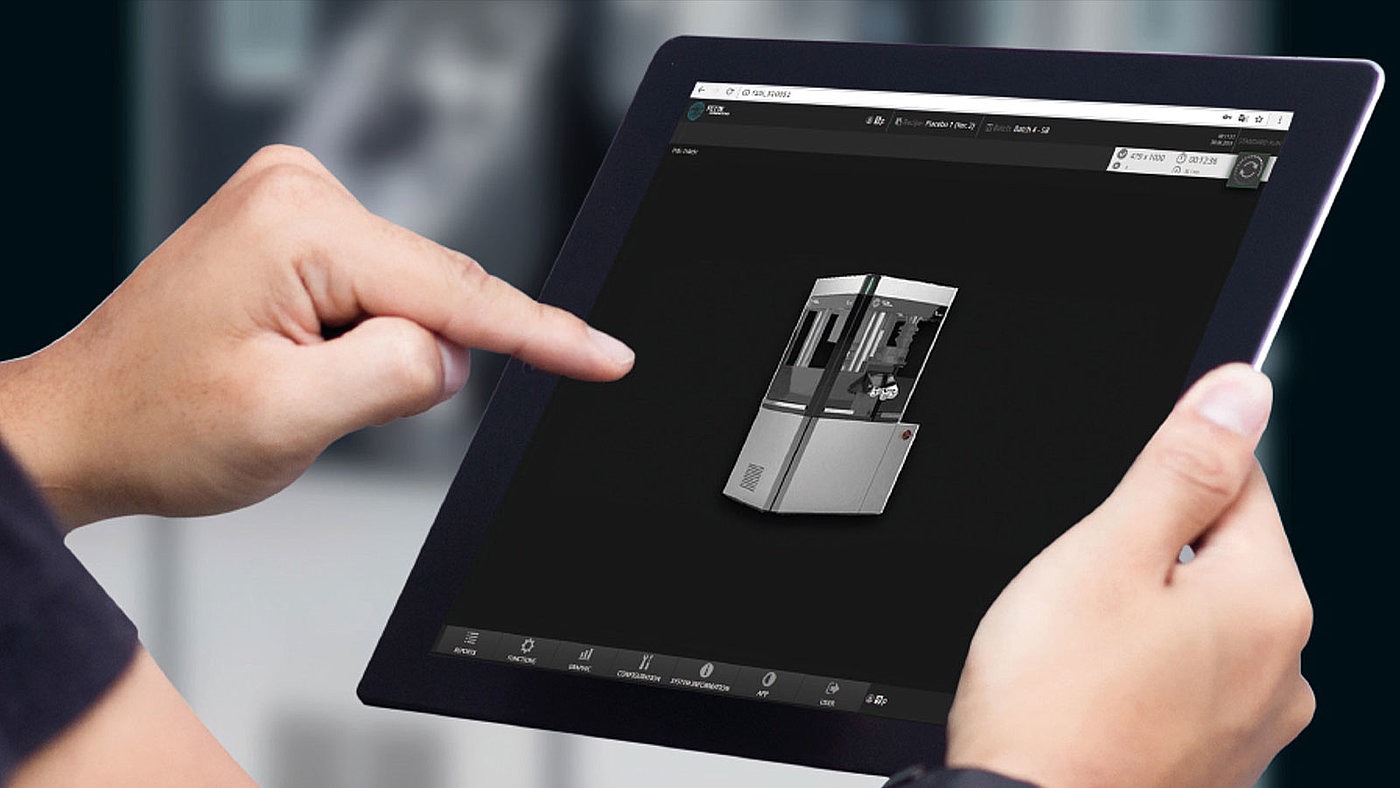
Pharma 4.0 is the vision of cross-production connectivity – a scenario which interlinks the pharmaceutical manufacturers’ machines and plants as well as linking them with suppliers and partners along the supply chain. This makes it possible to optimize processes and adapt them more flexibly to the new requirements of personalized medicine. In many places, however, the greatest obstacle facing connectivity in the Internet of Things (IoT) is the high degree of complexity displayed by production processes. The solution lies in plants with digital connections which can be easily integrated in existing production lines without requiring any major revalidation.
This is what Fette Compacting has achieved in the new i Series where practically all of the previous generation’s system assemblies of process and validation relevance have been retained or improved. As a result, the new plants are compatible with existing models. At the same time, they can be easily connected via plug-and-play using OPC UA interfaces, the standard for exchanging data in service-oriented architectures, with manufacturing execution systems (MES), and IoT platforms.
Machines and components communicate with each other – RFID
In Industry 4.0 factories, all components and products are attributed a unique digital identity for steering them contactless and automatically through the process. The key technology required for this is Radio Frequency Identification (RFID). By transmitting and receiving high-frequency radio waves, the fully-automatic F10i single rotary tablet press, the first machine in the i Series, identifies process components using a non-contact transmitter-receiver system and compares it with recipe formulations which have already been set. Using an electronic label, the tablet press “detects” the appropriate fill cam for each product, for example. The possibility of incorrect settings can therefore be eliminated. Mechanical settings can be stored in the recipe using RFID, enabling the plant to be swiftly and safely configured for each new product, which leads to savings in time and money when setting up the tablet press as well as a higher level of process reliability. A coding element can be used to reproducibly adjust the tablet scraper, for example, across an axis. This facilitates operation and increases precision during scraping as well as process stability. Recipe-specific reproducible adjustment via RFID reduces product loss, increases output and machine availability, and guarantees a consistent tablet quality.
The filling curves of the tablet press F10i are equipped with an RFID function. This enables the machine to recognize the matching filling curve for each product.
Entirely clean and safe
The increased use of active pharmaceutical ingredients (API) in particular will require dust-proof production equipment in the future. For this reason, the new tablet presses offered by Fette Compacting are consistently dust-proof as standard. To this aim, the tablet discharge, for example, was entirely revised so that it is now fully dust-proof. Depending on requirements, the plants can be equipped with glove ports and double safety barriers on the window flaps. Thanks to the fully-automated tableting process, containment is continuous – from filling the machine to the removal of tablets. Employees do not, therefore, need to wear any special protective suits. Accordingly, the containment option offers a high degree of operating safety which is perfectly coordinated to the requirements in production. The revised machine design also facilitates cleaning as it reduces the proportion of cladding surfaces to be cleaned by around 70 percent. As a result, the new tablet press improves workplace quality and employee protection while reducing cleaning to a minimum.
Digital eye on production
Another key feature of Industry 4.0 production environments is represented by real-time recording and analysis of production data – a function offered by the new i Series with the aid of the SmartInterface solution. Server-based real-time monitoring permits around-the-clock insights into the production processes via a mobile device. Via a secure intranet connection, everyone involved in production can monitor the full process documentation regardless of their location or platform and at all times on a smartphone, laptop or tablet. The application is available on all standard web browsers via the in-company network. Without having to be directly on site, this enables production managers to obtain an overview of the current production and machine status, deploy personnel more efficiently, and take immediate action in the event of faults. A dashboard displays all of the key performance indicators enabling immediate detection of deviations from standard settings. This also reduces the risk potential in the case of containment. Process values for analyses can be recorded, exported, printed, and signed without anyone needing to enter the production area. Using the browser application, operators, maintenance technicians, and their supervisors can utilize data for intelligent and swift decisions in order to increase overall production efficiency.
Pharma 4.0: from the machine to the production platform
With the aid of digital compatible tablet presses which can be integrated in interconnected production systems, pharmaceutical manufacturers can take a step into the digital age which no longer focuses on individual machines and plants but rather entire processes and supply chains. Considering the complex regulations and processes involved, the path toward Pharma 4.0 is still a long one. But the use of plants increasingly deploying sensors and software will gradually lead to processes which are increasingly automated. Pharmaceutical manufacturers can already benefit from the advantages today, i.e. reacting flexibly to changing requirements, changed product pipelines, new substances, and trends.