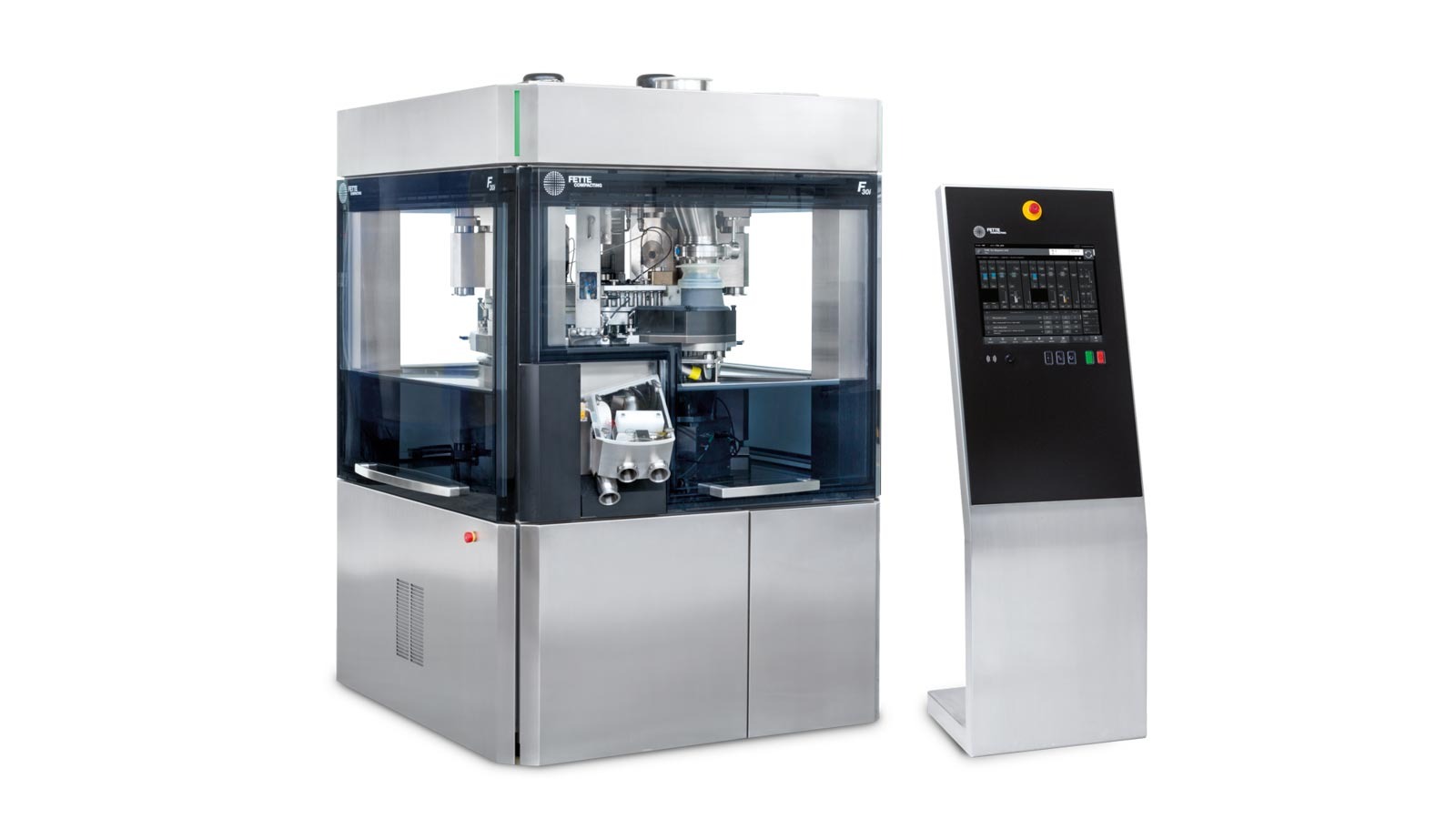
Mr. Friedrich, what differences are there between the F30i and the F10i?
Friedrich: The F10i is designed for the production of smaller batches while the F30i is a double-sided-rotary press for large volumes with a maximum output of up to 1.6 million tablets per hour. Furthermore, it is optimized for the production of two-layer tablets. To this aim, it avails of extremely fast sampling of the first layer via which the tablet weight can be precisely monitored and regulated in order to reduce product loss to a minimum.
Mr. Gierds, what features must a tablet press have today?
Gierds: Operator protection is increasingly gaining in importance. This is no longer about merely protecting operators from active and highly-active pharmaceutical substances. Entirely dust-free workplaces are gradually becoming the standard. For this reason, the tablet presses in the new i Series are already consistently dust-tight in the standard variant – from the press room through to the connections between the machine and process equipment. The machine can also be equipped with an optional containment package for products with active or highly-active pharmaceutical substances.
What role is played by operator friendliness when it comes to the efficiency of a tablet press?
Friedrich: The rule of thumb is that the easier the machines are to operate, the more efficient production will be. Therefore, all machines in the new i Series ensure that even less experienced operators can avoid operating errors, whereby this is facilitated by the newly-designed terminal which permits intuitive operation of the machine and peripheral process equipment from a central point. Additional support is offered by our SmartInterface which enables production processes to be monitored in real time via mobile end devices.
How digital does a tablet press need to be in order to be fit for pharmaceutical production in the future?
Gierds: Connectibility is an essential factor for Pharma 4.0. For this reason, the F30i and F10i feature all of the technical prerequisites for state-of-the-art production environments, including process equipment integrated via plug-and-play. The open interfaces meet the usual automation standards and permit easy connection to both a Manufacturing Execution System and the Internet of Things.
Considering all of this digitalization, are the mechanical components offered by the machine even of relevance?
Friedrich: Definitely! The mechanical design continues to harbor lots of potential for efficiency. For example, we have reduced the overall surface of cladding parts to be cleaned on the F30i by 74 per cent which shortens the cleaning time and saves costs in the process. Furthermore, formula-specific and reproducible hardware settings make it possible to reduce product loss and achieve improvements in output. For example, all of the machine's pneumatic settings can be made via manometer from a central operating panel. The values are then saved as parameters in the software.
Gierds: Minor details can also make an essential contribution toward improving efficiency.
The upper tablet discharge on the F30i has been improved for an even more stable production process. It now includes a specially-shaped pipe support which features an optimal geometry for the tablet flow. At the same time, an improved product wiper ensures that the machine can be easily adjusted to a wide variety of products and is even capable of handling complex tablet shapes.