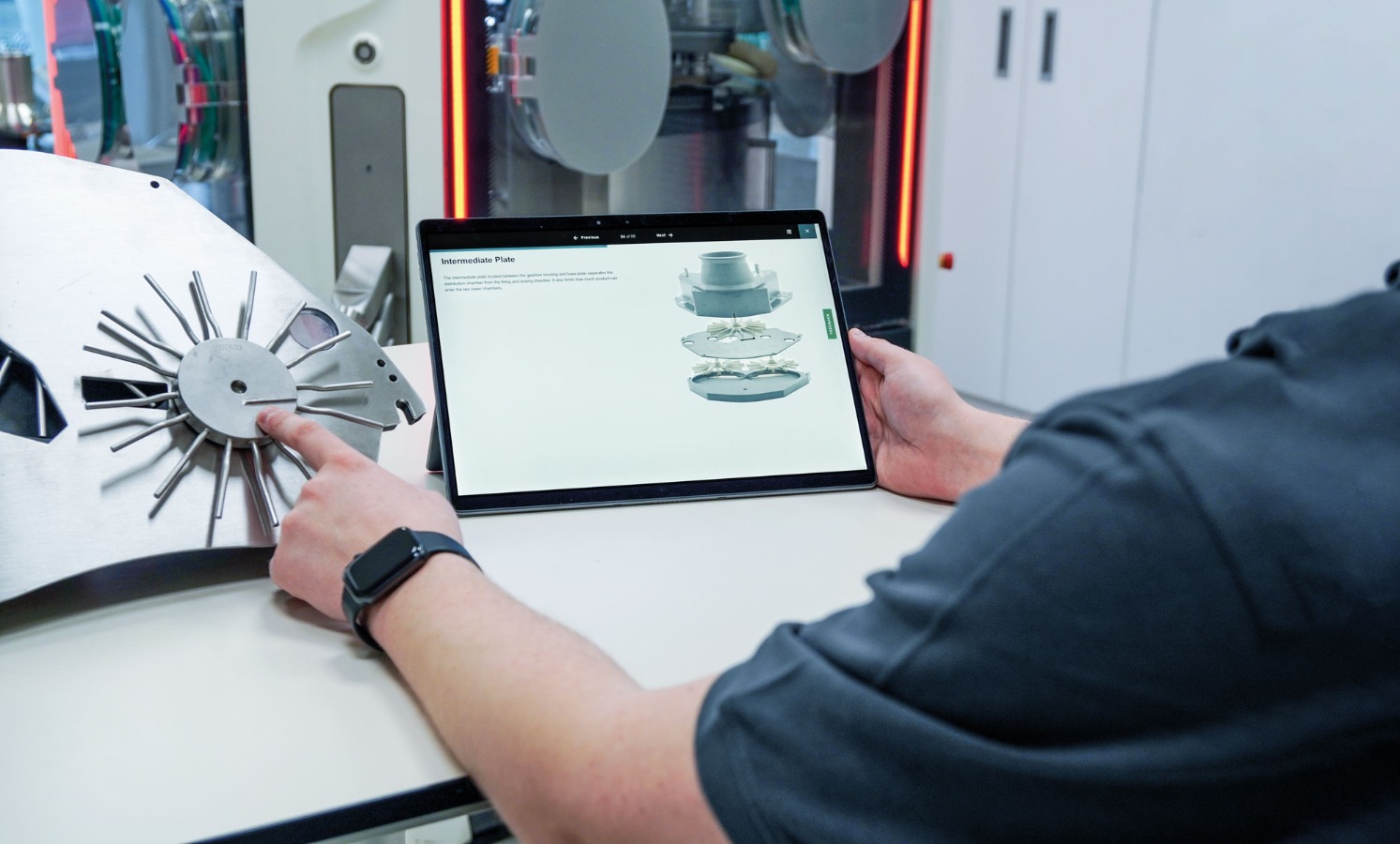
Fette Compacting’s business unit OSDi develops digital solutions to make solida production easier, safer and more efficient. Its name combines Oral Solid Dosage with digitalization. Among other things, the team is working on apps that support training and troubleshooting, manage performance, cleaning and maintenance based on data, and enable mobile access to all machine data.
The learning app, alva, was recently launched on the market. With up-to-date knowledge from experienced full-time trainers from Fette Compacting, it helps to qualify employees to work on tablet presses. “Users can expect vivid 3D graphics, animations and easy-to-understand explanatory texts in an app that is intuitive to use,” explains Britta von Selchow, Head of Digital Product Innovation at Fette Compacting. “And the best thing is that as browser-based software, alva is always available on stationary PCs, as well as on mobile devices. This means that users can access expert knowledge directly in the machine room, for example - always with the comforting feeling that they are doing the right thing on the machine. To express this flexible availability, the name of the app is derived by the phrase always available.”
Assemblies and functions at a glance
alva is divided into knowledge modules, each of which presents an assembly group. The app shows how the individual components work together and what their central functions are. Once users have completed a module, they can check their knowledge in a test and document their understanding of the content.
“Intuitive usability and conveying the most relevant detailed knowledge played a key role in the development,” says von Selchow. “The learning content aims to offer thematic depth and accompany the user through clear and easy-to-understand features. Accordingly, alva is taking a new approach, as conventional learning apps are often not detailed enough, yet overloaded with numerous functions. With OSDi’s tool, users can now concentrate on the essentials. In addition, the software ensures that users always receive up-to-date, first-hand information. This also prevents outdated information from being passed on.”
Professional photos illustrate components and functions. With the aid of the descriptions, even new employees know how to proceed when dismantling individual parts.
Close to the needs of users
In order to make the learning tool practical, the OSDi team used the agile methods of design thinking and lean start-up in its development. Both approaches ensure that products are developed in close consultation with customers. In design thinking, software developers start with a real problem and move forward step by step. OSDi develops initial prototypes, asks customers about their impressions, and takes them into account in the subsequent development steps. With lean start-up, the team makes sure to learn something from each attempt for the following development step. In combination, these two methods ensure a high degree of customer benefit and a manageable risk, because users advance iteratively and are always oriented toward the actual customer needs.
Initially, alva has nine modules that can be used for all tablet presses. “In addition, the app will be continuously equipped with new knowledge, for example with content for specific machine series and different user groups,” von Selchow promises.