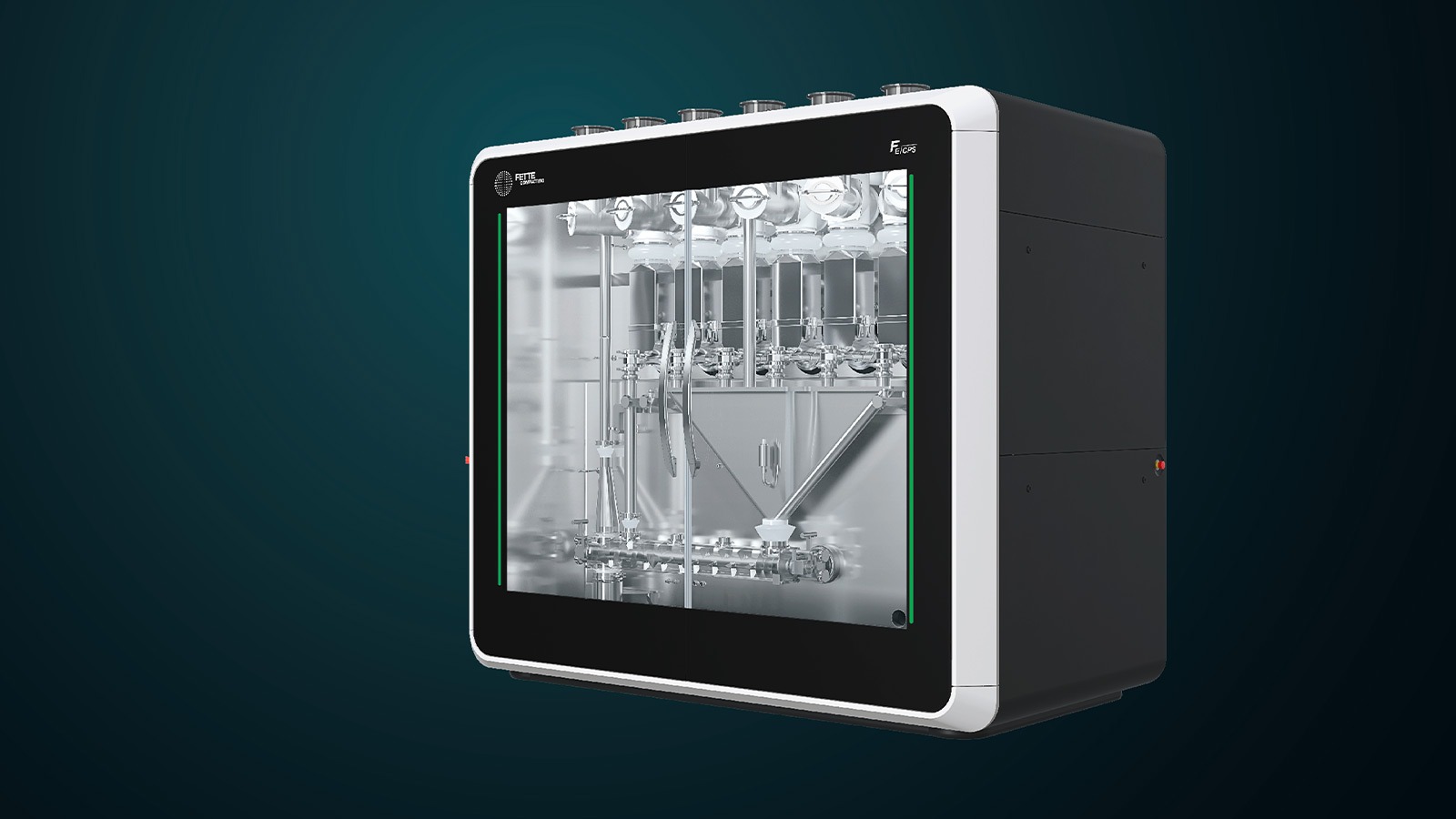
Continuous Manufacturing has been making its way into pharmaceutical and nutritional production for more than 15 years. It is associated with a wide range of advantages: Integrated processes increase efficiency and process reliability; process duration is shortened compared to batch processes, while the specific production output increases; formulaiton development can be done using far less API; market launches can be realized more quickly and production becomes more flexible overall.
In tableting, direct compression in particular is meeting with growing acceptance, as it enables a leaner plant design compared to granulation-based production. But that is not enough! Despite these advantages, many tablet manufacturers still have reservations. Concerns about potentially high costs and complexity continue to weigh too heavily.
All contaminated product contact parts can easily be removed from the process area for cleaning. This way, the process area can be completely emptied, making it very accessible and easy for an extremely fast cleaning.
Too large and too expensive?
A look at the typical pain points shows where the greatest development potential lies. For example, it can be observed that existing continuous plants require a large footprint and room height, which usually requires modifications to existing buildings or even entirely new builds. In addition, there are concerns about long lead times for equipment design and production, and investments tend to be high as systems need to be customized and require high facility investments. Many manufacturers are also put off by the complexity, as scientific personnel are required for set-up and specially trained operators. Interested parties also fear long downtimes during operation due to the time-consuming cleaning and product changeover processes. All in all, these reservations hint at high investment and operating costs.
The entire system can be integrated into existing production areas on just one level, so that building investments are reduced to an absolute minimum.
However, solutions for economically viable Continuous Manufacturing can also be derived from such criticism.
In essence, it is about a system that is less complex and easier to install and use thanks to a standardized, generic, compact and modular machine design. The direct compression process already creates optimal conditions for this, because upstream granulation processes are eliminated. The actual production process consists of only three or four steps and relies on less equipment. In addition the remaining unit operations should be re-designed and re-arranged in a fully integrated compact machine design. Direct compression also opens up more flexibility and faster product changes thanks to its lower degree of technological complexity. On this basis, the task now is to significantly reduce complexity once again and dare to take a technological leap. Raise the curtain for a world premiere!